Foundry Division
Foundry Division is specialized in manufacturing of Chilled Cast Iron components of Camshafts, Balancer shafts, Valve Tappets and Hydraulic lifter bodies used in the Gasoline and Diesel Engines.
- Foundry is spread over 25,000 Sq.Mtrs Area
- Manufacture upto 1.1 Meter Long Camshaft
- Camshaft Casting Weight upto 30 Kgs
- Separate Melting system for Camshafts and Tappets
- Green Sand, Shell and Cold Box Moulding
- Auto fettling Facility
Quality Management System
Foundry is IATF 16949 & ISO 14001 Certified for its Quality and Environmental Management System. It applies to the processes that create and control the products and services in an organization supplies. It outlines systematic control of activities to ensure that the needs and expectations of customers are met.
Material Capability
Chilled Grey iron, Chilled Ductile iron, Ductile Iron and Hardenable Iron. The material configurations are generally as per customer requirement.
Since inception, the Foundry has been vital to SAC’s self-sufficiency and growth and it is equipped with the following essential facilities:
Moulding
Green Sand Moulding
- High Pressure Squeeze Moulding (DISA ASPA 500)
- Simultaneous Jolt-squeeze Moulding (ARPA 450 – 1 Line)
- Simultaneous Jolt-squeeze Moulding (ARPA 900 – 1 Line)
- Two Sand System (Facing Sand & Backing Sand)
Shell Moulding
- Four Station Shell Moulding Machine
- Single Station Double door Shell Moulding Machine
- Single Station Single door Shell Moulding Machine
- Rotary table Oven
- Stationary table Oven
- Cold Box Moulding for Cam followers
Melting
Medium frequency Induction Melting System
- One 1000 KW / 1000 kg Furnace
- Two 450 KW/500 Kg Furnaces
- One 1000 KW/Tritrack/500 Kg Furnace
- Manual Closed Loop Pouring System
- Mechanized liquid metal handling System
Capacity
Products | Capacity |
---|---|
Camshafts and Valve Tappets | 15600 Metric Tons / Annum |
Pattern Shop/Tool Shop
SAC is having full-fledged pattern/ tool making facilities and all the tools are being made in-house. This unique facility shortens our new product development and good support to the Foundry production.
Measuring Equipment – Foundry
The process of Quality plan is spread out in number of stages which begins with the selection of pattern equipment and ends with the finished products, flawless in every detail. The latest quality assurance equipments and methods monitor every stage of the process.
Chemical Analysis
Optical Emission Spectrometer – 21 Elements (Thermo Scientific)
Thermal Analysis
ITACA Thermal analysis system
Sand Control Laboratory
- Sand Rammer
- Green Compression Strength Tester
- Green Shear Strength Tester
- Wet Tensile tester
- Moisture Tester
- Permeability Tester
- AFS Sieve Analysis Unit
- Active & Dead Clay Determination Unit
- Hot and Cold Tensile Strength Tester for Shell Sand
- Loss on Ignition and Volatile Matter Testing Unit
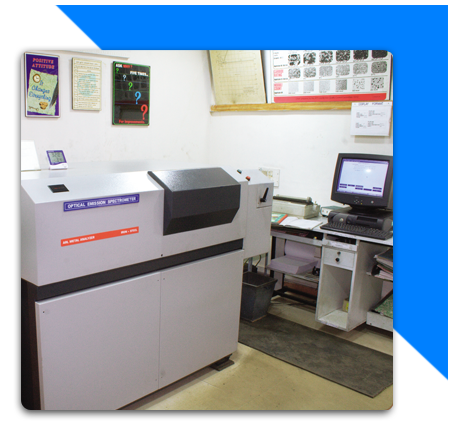
Metallography Laboratory
- Complete metallographic specimen preparation equipment.
- Microscope with Image Analysis and metallographic picture printing & transmission units
Physical & Mechanical Laboratory
- Brinell Hardness Testing Unit
- Digital Rockwell Hardness Testing Unit
- Digital Vickers Hardness Testing Unit
- Automatic & Computerised Ultimate Tensile Testing Unit ( UTM )